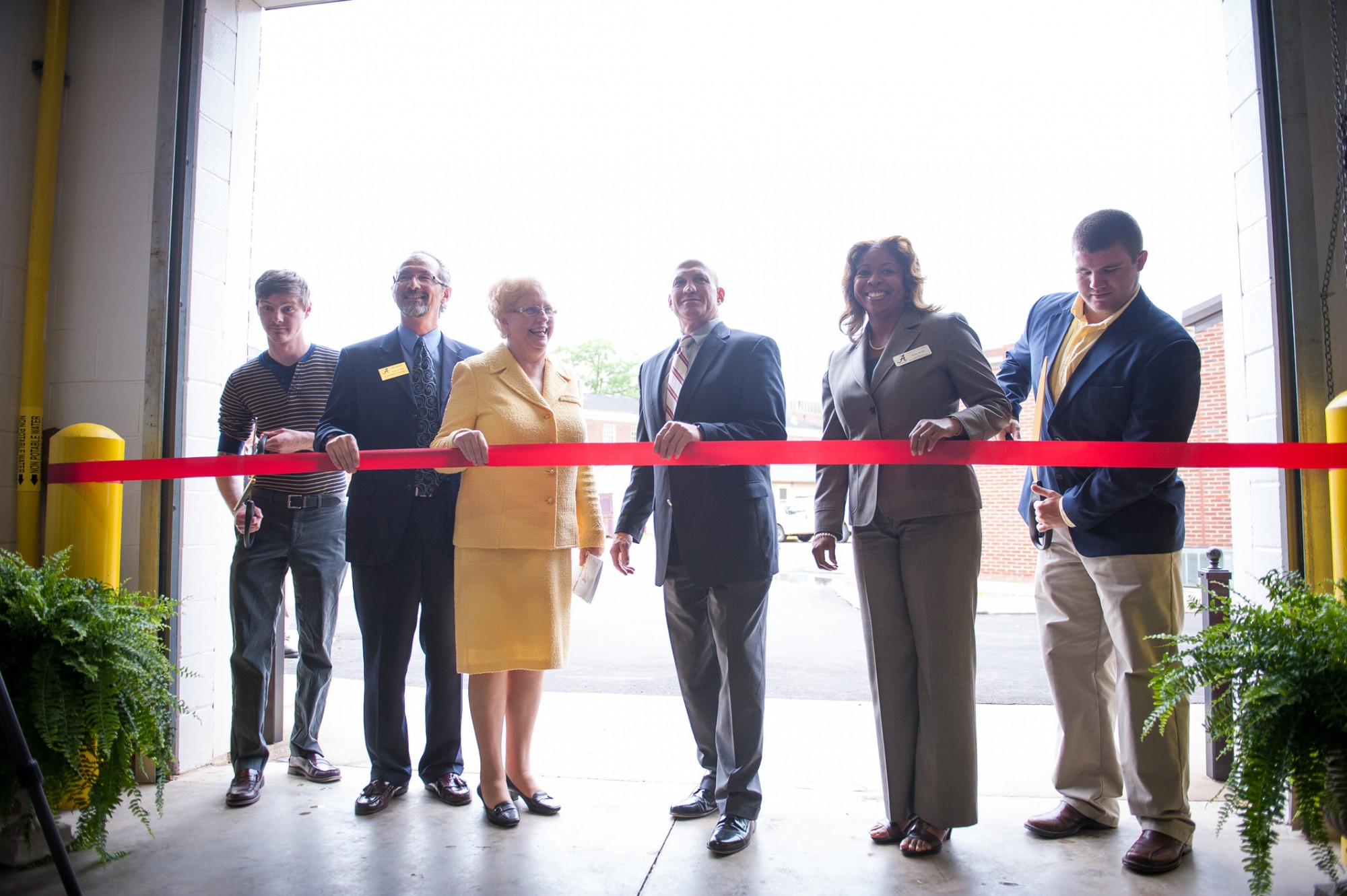
From left, University of Alabama student James Davis, College of Arts and Sciences Associate Dean Thomas Wolfe, UA President Judy Bonner, College of Engineering Dean Charles Karr, metallurgical engineering and materials head Dr. Viola Acoff and engineering student John Calhoun cut a ceremonial ribbon to a new foundry that puts art and engineering students in a shared space to spur creativity.
With the snip of a ribbon, The University of Alabama opened a new foundry to encourage creative collaboration between engineering and art students.
Located between Hardaway Hall and the old Bureau of Mines building, the foundry provides space and facilities for teaching, research and service to metal-casting and processing industries for students in the College of Engineering. The facility also adjoins a foundry used by the College of Arts and Sciences, and students from both colleges will share expanded and renovated collaborative space.
“I am excited about the opportunities the new joint-use foundry will present our students,” said Dr. Charles L. Karr, dean of the College of Engineering. “I strongly believe students from the arts and engineering can learn from each other. This space allows our students to enhance their creativity, and it is a plus for our College.”
Not only will there be opportunities for collaborative work, but the close proximity of the new facilities enhances resource sharing. Students and faculty in both colleges will learn from one another about the different kinds of investment, or mold-making, processes, as well as how to work with additional kinds of metals and alloys for different purposes.
“The Bureau of Mines’ art and engineering complex will be a space where any student can come create something,” said Dr. Robert Olin, dean of the College of Arts and Sciences. “This space is meant to provide a place for inspiration and encourage our students to develop their great ideas and turn them into reality. We want them to have somewhere they can get their hands dirty and experience the enjoyment of seeing a project come to fruition.”
Still, at its heart, the foundry serves the needs of the metallurgical and materials engineering department since it replaces the foundry in a part of H.M. Comer Hall razed to make way for the North Engineering Research Center.
“I am pleased we were able to construct our new facility because our students get a leg up on other graduates from across the country due to their experiences in our foundry,” Karr said.
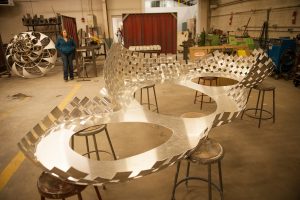
and arts and sciences.
The UA metallurgical and materials engineering department is one of just eight metallurgical engineering programs accredited by the Accreditation Board for Engineering and Technology, and it is one of only 20 Foundry Educational Foundation Certified Schools in North America.
“Having a fully functional modern foundry is vital to us being able to maintain our ABET accreditation as a metallurgical engineering program,” said Dr. Viola Acoff, head of the department of metallurgical and materials engineering.
With about 5,000 gross square feet, the new foundry will incorporate all basic types of equipment used in operating foundries, and it permits demonstration to students of most of the practices encountered in making cast iron, steel and nonferrous alloys.
Equipment highlights include the following:
- three Inductotherm melting furnaces for melting cast iron, steel, brass, bronze and aluminum-based alloys
- a NASA withdrawal furnace for melting and casting superalloys under vacuum that can produce up to 25-kilogram turbine components cast into ceramic-shell molds
- molding equipment and a core machine for making green sand and pepsetbased molds and cores
- finishing equipment
- spectrometer by Spectro Analytical Instruments
- an investment casting lab with a 3D printer “Thermoset” by 3D Systems for making investment patterns
- a sand-testing lab and a dedicated computer lab where students can perform mold and casting design using advanced casting and ingot simulation software tools
The withdrawal furnace was acquired by the department a few years ago from the NASA Marshall Space Flight Center, but it could not be installed in the old foundry. The state-of-the-art furnace is used by aerospace companies to make aircraft engine components typical on commercial passenger jets.
“With this additional capability, students will be exposed to every major type of casting process, ranging from traditional casting of cast iron to the casting of nickel-based superalloys used in various aerospace applications,” Acoff said.